Custom fabrications come in all shapes and sizes at Ameritex, from items that fit in the palm of the hand to massive sheet metal assemblies requiring an oversized load permit to ship. No matter what comes our way, we put our heads together to figure out how to get it done in a timely fashion.
Still, some projects are inevitably more challenging than others, and large assemblies and components definitely fit into this category.
How Big Is Big?
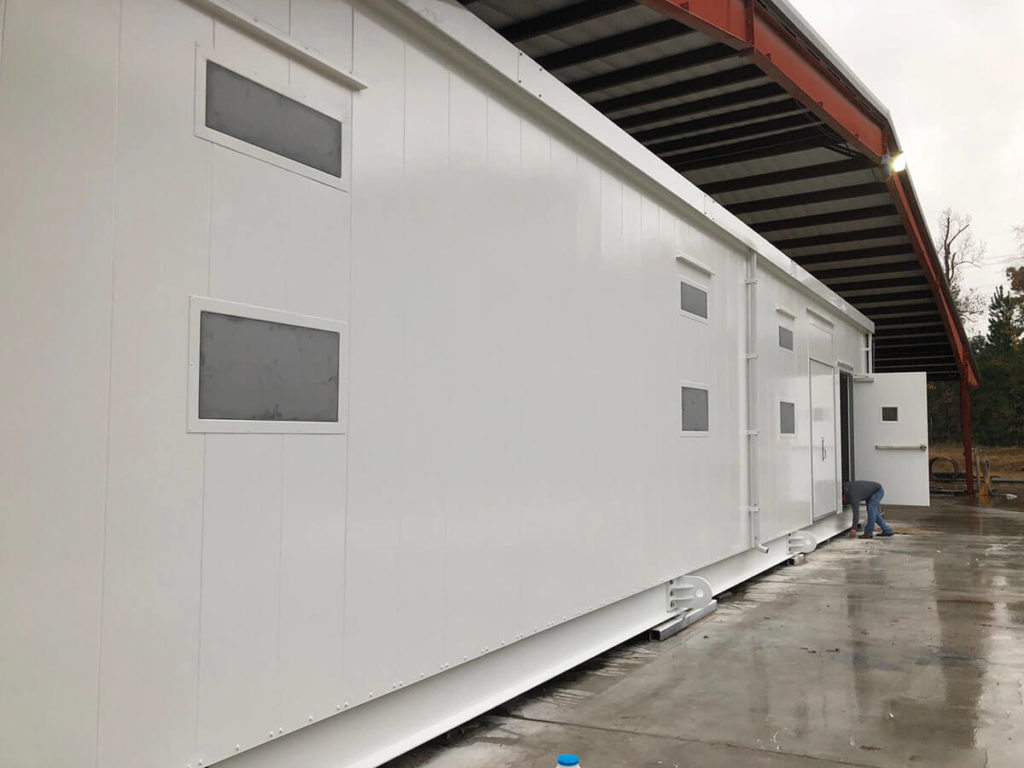
We begin classifying items as “large” when they don’t fit on our 4’x8’ tabletops. When sheet metal assemblies and parts are big enough that 2-3 workers cannot move, flip, or rotate them easily, extra foresight is required to control costs, lead times, and quality.
So before designing your next operator cabin, enclosure, large structural weldment, or other big part or assembly, get familiar with these general guidelines.
Guidelines for Designing XL Sheet Metal Parts and Assemblies
1. Break assemblies into sub-assemblies
The #1 rule when designing a large sheet metal assembly is to break it down into as many manageable sub-assemblies as possible. Allowing fabricators to work on smaller tabletop-size sub-assemblies and combine them at the end of the project creates the smoothest build.
As someone wise once said, the only way to eat an elephant is one bite at a time. If you think about the process of framing a house, a framer doesn’t start by standing up individual pieces of lumber; they build out entire walls flat on the ground where they aren’t fighting gravity, then stand the walls up into place. Fabricators are most efficient when sheet metal assemblies follow this same logic.
2. Consider all options for joining parts together
The bigger the sheet metal assembly, the easier it is to overlook the details. All too often, designers treat how the assembly goes together as an afterthought, defaulting to the assumption that fabricators can just weld the parts.
But welding isn’t always the best option. In fact, our team lives by the mantra, “If you can bolt it on, you should bolt it on.” Fasteners are equal in strength to welding and have the added benefits of being more cost-effective and easier to replace. In some cases, fastening may be the only option if the location of the part is unreachable to welders.
3. Ensure complex sub-assemblies are complete and operational outside of the main assembly
When designers are building items like enclosures into the wall of a sheet metal assembly, they often use parts of the larger assembly to create the exterior of the enclosure or hinge the door. In our experience, this approach always leads to trouble.
A better alternative is to build the enclosure separately and ensure that it’s 100% operational outside of the main assembly before bolting or welding the unit in place. The same logic applies to consoles, pedestals, racks, kiosks, doors, and displays.
If you have an XL sheet metal assembly project coming up and could use our expert input on your design, we’re more than happy to help. Reach out today for a design consultation.