How can we effectively punch, bend, tap, and form all on a single machine?
Using none other than our LVD PX-1530 punch press.
Punching may be an old school technology, but our new school equipment and highly experienced operators make this capability the best choice for certain custom fabrications.
When to Use Sheet Metal Punching for Custom Fabrications
Punching, which involves exerting a high amount of pressure to remove material from a piece of sheet metal, is ideal for medium to high quantities of sheet metal parts with simple geometries or parts with formed features.
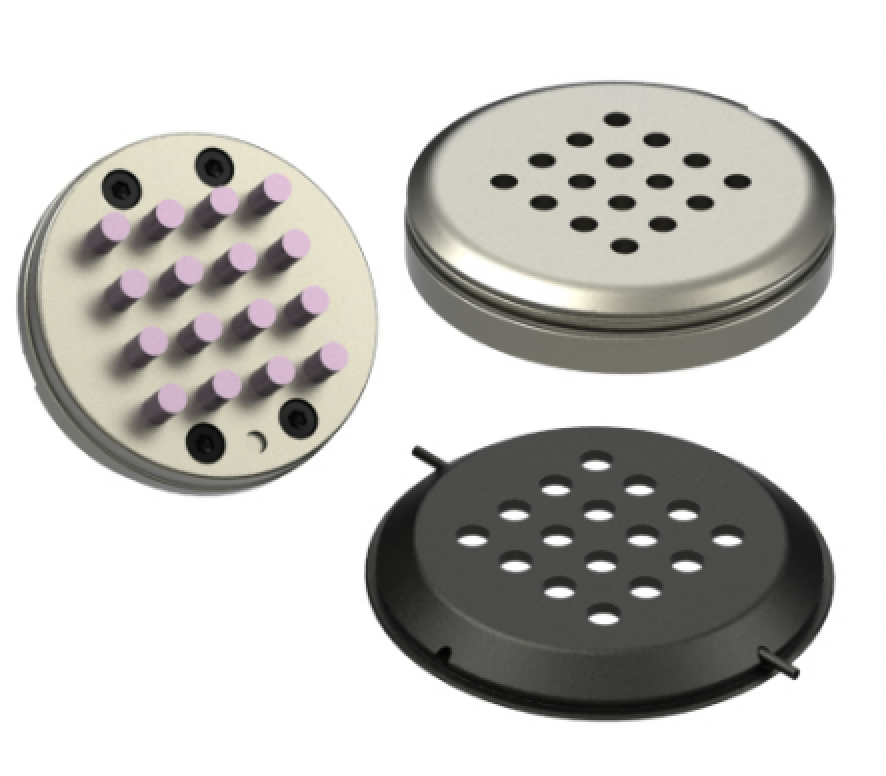
Let us explain.
We’ll start by highlighting the major drawback of punching: the setup is time-consuming. While this con makes punching cost-prohibitive for one-off parts, it’s fairly easy to justify the setup time once you’re dealing with higher quantities.
Why? Because running a punch press like ours is relatively inexpensive, and our machine combines processes to eliminate downstream operations like tapping, hardware insertion, or even bending.
Our punch press can extrude features onto a part, add critical fastening points, and bend flanges up to 3” tall—all with minimal human intervention. What does this mean for customers? It means you benefit from a more reliable process and reduced costs and lead times.
It’s important to note that punching can become expensive if you need custom tooling, so we generally recommend this capability for parts requiring sizes and shapes that we can achieve with our standard tooling.
Our machinery partner, LVD, made an excellent demonstration video showcasing the versatility and efficiency of the LVD PX-1530 punch press, which is capable of handling even complex, three-dimensional parts. Check it out here.
We encourage you to reach out to us with custom fabrications that are a good fit for our punch press. We would love to work with you to create a part that perfectly fits your needs and budget. Request a quote today, and we’ll respond within 24 hours.