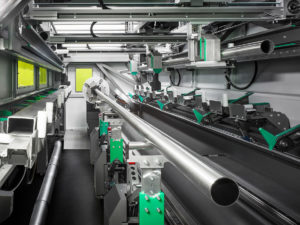
When your custom fabrication requires metal tubes or structural members, tube laser cutting is the best bet for speed, precision, flexibility, and accuracy.
This automated machining process, which involves cutting tubes of various shapes to specified lengths or lasering patterns into tubes, is much faster and more effective than alternatives like sawing through tubes and manually drilling holes.
However, as with any manufacturing method, there are standard best practices to follow when requesting tube laser cutting services.
How to Design a Tube Laser Part That Works for You and Your Fabricator
When we talk about designing a custom fabrication that works for you and your fabricator, what we really mean is that we want to ensure that you get exactly what you want as quickly and cost-effectively as possible. Here are five tips for accomplishing this goal when you need tube laser cutting services:
1. Watch the weight
Most tube laser cutters have a maximum weight capacity, and it’s important to design your parts with that number in mind. At Ameritex, our maximum capacity is 27 pounds per foot.
Fabrication shops tend to no-quote tube laser parts that are too big for their machines because the risk of damaging the equipment is too high. There is the option to run the tube laser cutter more slowly to accommodate a larger part, but that typically means increasing the price.
2. Allow space for an initial cutoff and subsequent part-offs
Be sure to design your tube laser part slightly shorter than the raw material. Your fabricator needs to make an initial test cut to ensure the laser settings are dialed in correctly.
Trimming the ends of the material also enables fabricators to create a nice square edge. This step is often necessary because most raw materials that come from a mill do not arrive with perfect edges and won’t meet customers’ standards.
In addition to the initial cutoff, fabricators also need space to “part-off” the material from one part to the next. Leaving a total of 6” of raw material is generally enough to allow for cutoffs and part-offs.
3. Tolerance tube laser parts from the center
The larger the diameter of the structural piece, the more likely it is that the raw material will have significant tolerance variations. While these variations may comply with ASTM standards, failing to accommodate them in your design may result in the part being out of tolerance.
When you need tight tolerances, one easy solution is to dimension tube laser parts from the centerline instead of the outside edges of the structural piece.
4. Avoid over-tolerancing tube laser parts
If you can be flexible with tolerances, avoid making them unnecessarily tight. In many cases, customers’ software automatically defaults to clearance hole sizes that are more appropriate for machined parts. These holes are often smaller than what the part actually requires.
We’ve had great success making bolt holes on structural weldments ⅛” larger than the bolt used to fasten the assembly—you’ll be pleasantly surprised to find just how easy it is to assemble these parts when they arrive!
Similarly, if you’ll be fastening a 500-pound structural assembly with something like ⅜” hardware, lining up the bolt hole pattern is significantly easier when you’re dealing with ½” holes instead of the standard machine clearance size of .386.”
5. Consider bundling materials
To ensure consistency across all your tube laser parts, consider bumping up the raw material quantity to whatever the minimum amount is for a bundle—typically 6,000-10,000 pounds. Material bundling is a great way to limit standard variations in the metal.
If you can commit to a higher quantity, talk to your fabricator to see what their local steel vendors have available in bundles for nice consistent cuts.
When you need tube laser cutting services, Ameritex is here to get you the exact parts you want. We recently added BLM Group’s LT8.20 tube laser cutter to our fleet of world-class equipment to improve cost, flexibility, and lead times for customers. Request a quote today!