In July 2021, Ameritex partnered with BeehiveFund, kick-starting an ongoing journey toward implementing lean manufacturing principles and practices in our precision sheet metal fabrication shop.
In the spirit of transparency, we committed to sharing frequent progress updates here on our blog. A few months ago, we wrote about the kaizen method and the 5S system, consisting of 5 pillars for facilitating better organization and order.
We began with Seiri (sort), Seiton (set in order), and Seiso (shine), combining our resources to get everything in our shop in clean, working order and into its rightful place.
We’re excited to share more updates with you today.
5S System Progress Updates at Ameritex
Standardize and Sustain 5S Audits Communication Process and
Electronic Boards
Seiketsu (Standardize) and Shitsuke (Sustain)
We organized 6 training sessions for each production department and presented the final 2 pillars—Seiketsu (standardize) and Shitsuke (sustain)—in relation to the first 3. Order and product centricity are at the foundation of any successful manufacturing operation, and the 5S system ensures that we have the right tools, materials, and information in all work areas.
- Standardize involves establishing guidelines to clarify the 3S conditions and implementing visual elements in the workplace via checklists, schedules, labels, signs, guiding lines, and shadow boards.
- Sustain consists of forming long-term habits to retain and increase the gains resulting from the 5S system. This phase includes audits and Gemba walks, ongoing support of 5S activities, and up-to-date communication. Supervisors and management are heavily involved.
5S audits
Kaizen prioritizes making small, gradual changes that are sustainable long-term, leveraging regular audits to measure and track performance. We deployed a rigorous 25-point audit for each work zone in our precision sheet metal fabrication shop that we conduct every 2 weeks. The audit incorporates 5 distinct elements to represent each S in the system.
Communication process and electronic boards
We launched a centralized communication process to ensure that everyone is up-to-date on performance metrics. After completing each audit, we publish the report for Ameritex supervisors via Microsoft Teams, allowing them to monitor performance within their departments easily. Production employees have access to an electronic 5S board installed in the breakroom that keeps them up to date.
Bettering Ourselves to Become Better for Our Customers
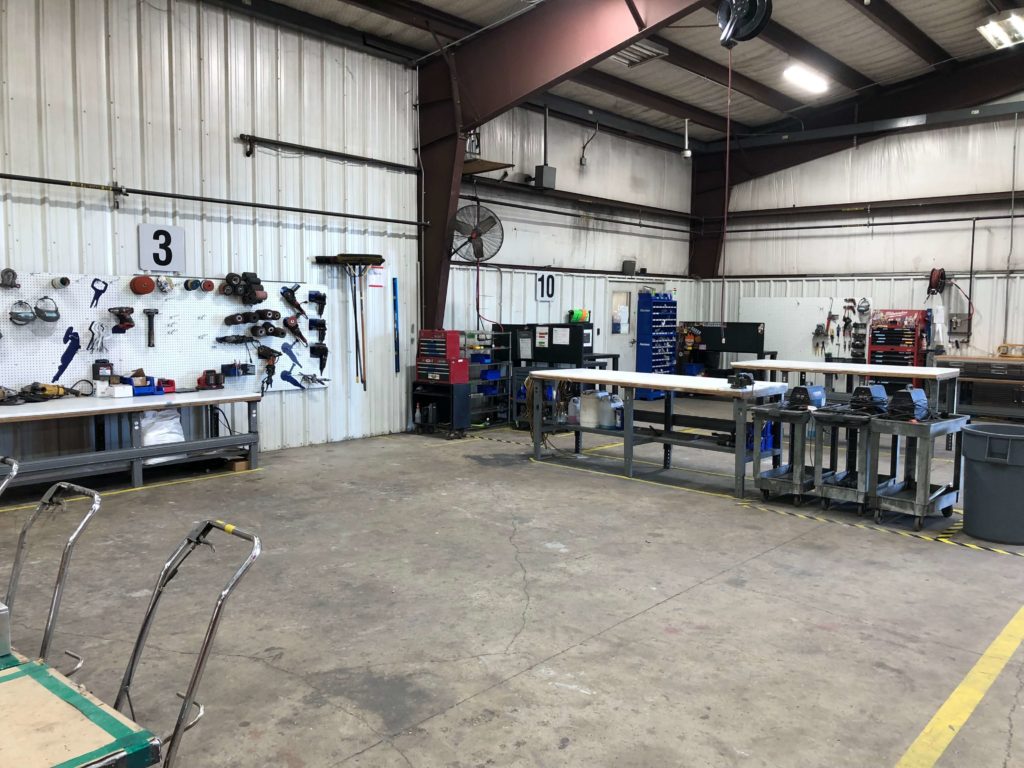
We’re pleased to share that we’ve seen excellent progress already, thanks in large part to our team members’ commitment to this lean manufacturing initiative.
The 5S system is a practical tool that our employees genuinely enjoy, as it allows them to perform their jobs safer, easier, faster, and better. We’ve even had some friendly competition as teams from different departments compete to out-perform each other.
Product centricity—a dominant pillar of lean manufacturing—has taken root as the guiding principle leading each department in our precision sheet metal fabrication shop. It enables us to serve each product that comes through our facility completely, accurately, and timely—a major win for our customers.
We have an exciting road ahead of us, and we’re glad to have you on this journey with us. Stay tuned for more updates, and don’t hesitate to request a quote if there’s anything we can do for you.