We recently highlighted several custom fabrications we commonly build here at Ameritex. In our new Product Highlight series, we’ll take a deep dive into each one of these fabrications, so you’re clear on our full line of capabilities and what to expect from us when you request metal fabrication services.
Without further ado, let’s begin with sheet metal fabricated tanks.
What Are Sheet Metal Fabricated Tanks?
A tank is any tightly sealed product used to store fluids. Unlike enclosures, which keep air or water out, tanks serve the purpose of holding fluids like water, oil, diesel, and even specialized cooling liquids for cryptocurrency mining equipment.
Material selection is critical for tanks because the material and any coatings (e.g., hot-dip galvanization, zinc coating, powder coating, paint) must withstand direct contact with the stored fluid. We often recommend stainless steel for its corrosion-resistant properties, but customers can request carbon steel or aluminum as less expensive options.
We use welding to seal tanks because it’s easier to achieve a tight seal with welding than with fasteners. One major advantage of a custom sheet metal fabricated tank is that you can have us weld flanges or piping to the exterior so that the tank bolts in place without requiring any drill holes.
Ameritex’s Rigorous Testing Process for Sheet Metal Fabricated Tanks
One thing that sets Ameritex apart from other precision sheet metal tank manufacturers is our commitment to rigorous testing to ensure no leaks in the weld.
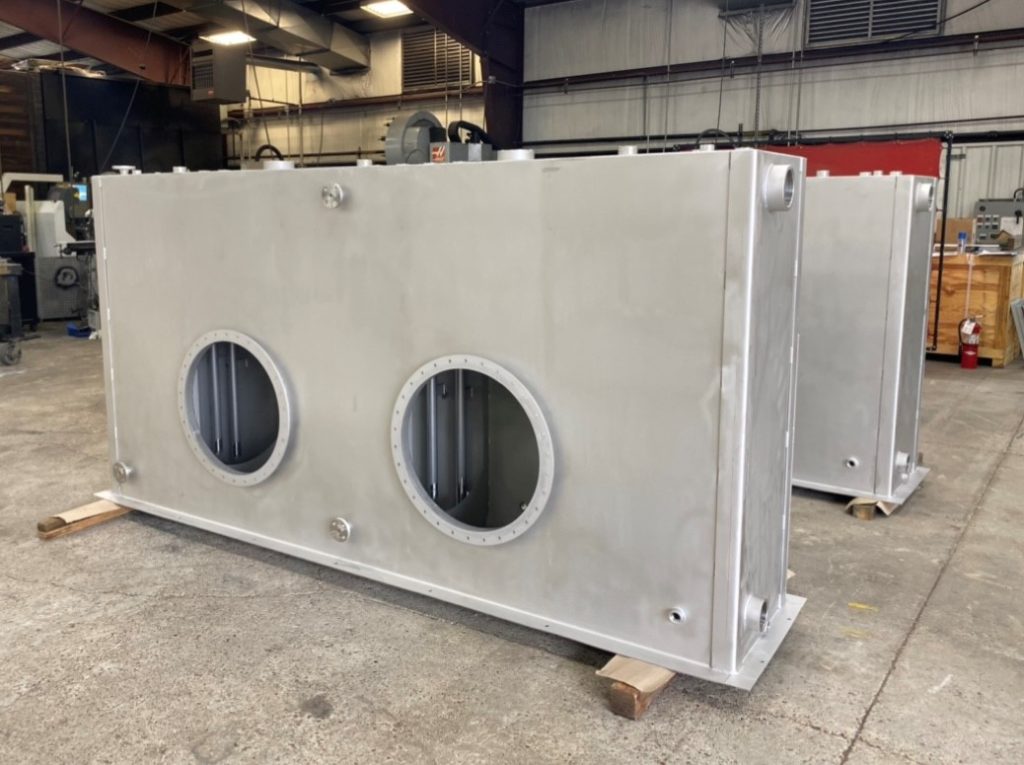
We begin with dye penetrant testing, the industry standard for ruling out obvious leaks. This test involves applying different colored liquid penetrants to the interior and exterior of each welded seam. The exterior penetrant draws the interior penetrant to its side, so if we see the color coming through, we know there’s a leak. We repair the spot where we identified the leak and then perform additional tests until we get it right.
The one downside to dye penetrant testing is that it’s a visual inspection process, meaning it’s possible to overlook the leaks. If necessary, we may follow up with one of these detailed testing options for sheet metal fabricated tanks:
- Air testing. This process allows us to test the air pressure in the tank up to a pressure rating specified by the customer. The caveat is that we must have a way to plug up any intentional holes in the tank’s structure first. If we can achieve and maintain the desired pressure rating, we’ll know there aren’t any leaks in the tank.
- Water testing. If the tank has an open top that isn’t sealable, we can conduct water testing as an alternative to air testing. We’ll plug any holes in the tank’s structure, fill the tank with water, and visually inspect it for any leaks. There’s even the option to dye the water to see it more clearly.
- Specific fluid testing. Certain oils are more viscous than water and may leak more easily through cracks. If you plan to store oil or another highly viscous fluid in your tank, we’ll conduct testing with the specific fluid in place of water for more accurate results. However, it’s important to note that we can’t test with diesel or gasoline.
If your sheet metal fabricated tank requires a level of testing outside our realm of capability, we’re happy to call in third-party inspection companies to conduct certified testing.
When you need precision sheet metal tanks, you need a shop like Ameritex that will go above and beyond to get you a superior product. Request a quote today!